Grinding for uniform surfaces
Professional polishing machines with abrasive belts or combined with brushes, for fast but indispensable metalworking processes.
Grinding, i.e. the removal of a certain amount of material from a metal part by grinding wheels or cloth belts used as an abrasive medium and having different grits depending on the type of abrasion to be obtained. Grinding, also known as sandpapering, is usually the first of the treatments carried out in machine workshops on cast or welded parts, which then have to be finished. The process of grinding metals, usually dry, is important for obtaining uniform surfaces because it smooths and removes roughness. It is usually performed by experienced and qualified personnel who have acquired a certain dexterity, sensitivity and precision. Indispensable if the part is to be subsequently painted. They often start with coarser grit belts or grinding wheels and then move on to finer grits to achieve more refined levels of roughness. The grinding operation can be repeated several times, depending on the quality of the starting surface and the desired result, in which case we speak of roughing, semi-finishing, finishing and superfinishing.
With the subsequent cleaning or polishing phase, all micro impurities are gradually removed from the material until it is perfectly smooth and shiny or matt, depending on the material. Productivity, as mentioned above, depends not only on the efficiency of the machine, but on the skill of the operator, how he or she uses the machine, their manual dexterity, their posture, the size of the belt or grinding wheel used.
MARPOL FR has a wide range for this type of small machine tool. Vertical, horizontal, adjustable belt machines, combined with brushes or bevelling machines for dry machining.
Write to info@marpolfr.com
for the contact details of retailers.
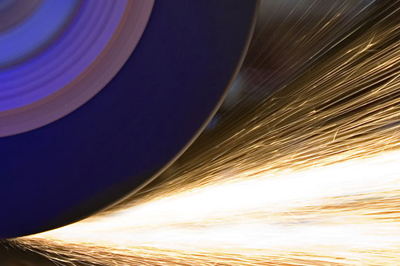